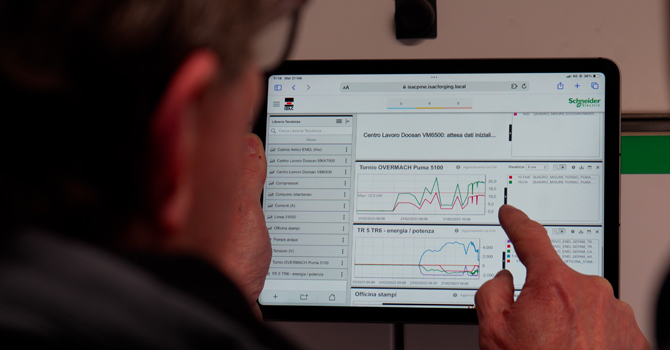
I.S.A.C, azienda che ha sede a Busano (TO) è specializzata nello stampaggio a caldo dell’acciaio. Attiva dal 1974, produce una vasta gamma di stampati di varie dimensioni rivolgendosi a molteplici settori e operando a livello nazionale e internazionale. I.S.A.C. nel 2019 ha avviato un progetto per sostituire i forni a gas precedentemente utilizzati con forni a induzione elettromagnetica e a suo tempo, per supportare l’aumentata richiesta di energia, si è rivolta a Schneider Electric per sostituire la cabina di media tensione con una nuova soluzione, in grado di gestire i 4.500 kW di potenza richiesti e dotata di connettività digitale.
A fronte dell’aumentato fabbisogno energetico, l’azienda ha deciso di adottare anche soluzioni per tracciare i consumi energetici, sfruttando i dati e la reportistica sia al fine di ottimizzare l’uso dell’elettricità, sia di poter disporre delle informazioni utili per la defiscalizzazione dell’energia.
ISAC ha quindi scelto il software EcoStruxure Power Monitoring Expert, a cui ha connesso il sistema elettrico e tutti i macchinari: i forni naturalmente, ma anche i compressori e le pompe dell’acqua necessarie per il raffreddamento. A distanza di alcuni anni, I.S.A.C. ha fatto il punto sui vantaggi ottenuti grazie a questo investimento per aumentare l’efficienza energetica complessiva, che ha aiutato anche a fare passi avanti in termini di sostenibilità. “Grazie al cambio dei forni usiamo energia elettrica che per il 40% proviene da fonti rinnovabili, mentre prima tutto era alimentato con l’energia fossile del gas. Inoltre questo tipo di alimentazione dei forni ha ridotto del 90% la nostra percentuale di scorie” dichiara Ombretta Grivetto, Consigliere Delegato di I.S.A.C.
EcoStruxure Power Monitoring Expert è una piattaforma progettata proprio per le aziende ad alto consumo e intensità energetica con l’obiettivo di massimizzare la disponibilità dei sistemi, l’efficienza energetica e operativa. La scelta fatta alcuni anni fa si è rivelata di altissimo valore per I.S.A.C. all’insorgere della crisi energetica, offrendo strumenti fondamentali per gestire la volatilità e l’aumento dei costi. Monitorare significa conoscere, conoscere significa poter prendere le migliori decisioni operative coniugando le prestazioni di produzione e il risparmio energetico.
Grazie a report automatici, generati a orari personalizzati e inviati all’attenzione del personale specializzato, la lettura delle variabili ha consentito di capire come e quando viene usata l’energia durante le lavorazioni in modo dettagliato e preciso, così da poter intervenire in modo puntuale là dove è possibile generare il migliore impatto in termini di riduzione dei consumi ed efficienza: in particolare, oltre che sui forni, sui compressori per le pompe dell’acqua. Il software, inoltre, permette di gestire efficacemente l’attività dei vari macchinari.
I.S.A.C ora può spegnere i trasformatori dei forni nei weekend, con un risparmio stimato di 200 – 250 kWh al mese. Conoscendo esattamente il consumo di energia generato dai forni in ogni fase di lavorazione, I.S.A.C. riesce anche a capire quanto incide la fase di riscaldamento sul prezzo finale di ognuno dei suoi prodotti; altre efficienze si sono ottenute andando a intervenire sul funzionamento delle pompe, che è stato ottimizzato usando inverter che ne regolano la portata e gestendo diversamente la loro attività. Prima esse venivano accese all’avvio della produzione e spente alla fine della stessa, senza alcun tipo di regolazione. Oggi invece è possibile gestire al meglio l’uso di questi componenti, che a pieno regime assorbono una potenza di 80 kWh, che scende a 35 kWh quando è in funzionamento uno solo dei forni.
“Grazie a EcoStruxure Power Monitoring Expert oggi siamo pienamente consapevoli dei nostri reali consumi. Questo software rappresenta uno strumento prezioso per prendere decisioni operative più consapevoli” ha aggiunto Ombretta Grivetto. Senza un accurato sistema di monitoraggio dei consumi e senza l’adozione di sistemi di distribuzione elettrica di media e bassa tensione dotati di connettività, nessuna delle informazioni necessarie a ottimizzare sarebbe stata disponibile e utilizzabile per le scelte operative in questo modo.